“Industry 4.0 is the biggest structural change of the past 250 years – a transformation of scale, scope, and complexity unlike anything humankind has experienced before.” - Henrik von Scheel, Management thinker & Mastermind of the European Digital Agenda
Industry 4.0
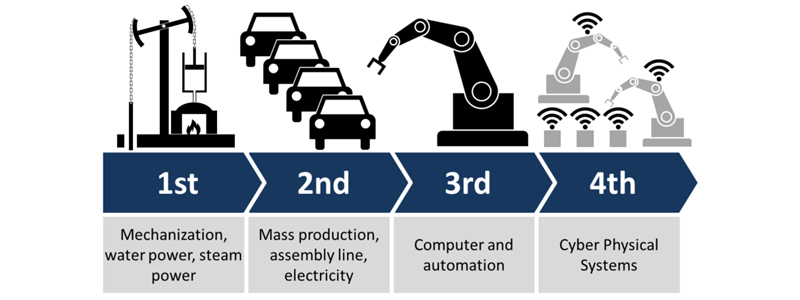
One of the recent buzzwords being widely spoken about is Industry 4.0, also popularly referred to as the fourth industrial revolution. The first three waves of the industrial revolution were headlined by the steam engine, assembly line & mass production, and automation facilitated through computers, respectively.
Industry 4.0 is the latest disruptive trend of automation headlined by Cyber-Physical Systems (CPS). It includes cutting-edge ICT tools and technologies such as autonomous robotics, business analytics, Industrial Internet of Things (IIoT), simulation, cloud computing, cyber security, additive manufacturing, horizontal & vertical system integration, Virtual Reality (VR), and Augmented Reality (AR). Complementary to Industry 4.0 is the integration of disruptive and game-changing technologies in the form of the SMAC - Social, Mobile, Analytics, and Cloud stack, which promises to be the next wave in enterprise computing. Industry 4.0 has realized the manufacturer’s dream of a "smart factory." Its transformational power comes from marrying advanced production and operations techniques with digital technologies to create connected enterprises that use data to drive intelligent actions in the physical world. Within these modular structured smart factories, cyber-physical systems monitor physical processes, create a virtual copy of the physical world, and make decentralized decisions. Interestingly these systems are fueled not by gasoline or oil or electricity but by ‘data’ and the capabilities to leverage and mine this data using machine learning and artificial intelligence. Manufacturing and production become adaptive, agile, autonomous, automated, collaborative, coordinated, connected, decentralized, fast, flexible, and intelligent resulting in greater operational efficiencies and lesser costs for enterprises.
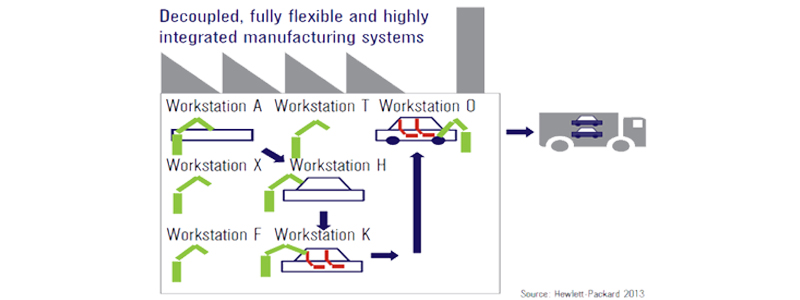
Over the Internet of Things (IoT), i.e., connectivity of physical assets, CPS communicates and cooperates with each other and with humans in real-time both internal & cross-organizational services are offered & utilized by participants of the value chain. CPS consists of collaborating computational elements controlling physical objects, whose processes are seamlessly monitored, coordinated, controlled, and integrated. An example would be a totally connected and retooled supply chain, which can reconfigure itself on receipt of any new data point. If a weather delay ties up a shipment, a connected system can proactively adjust and modify manufacturing priorities bringing about perfect alignment between supply chain planning and execution.
The origins of these technologies for manufacturing, collectively being referred to as Industry 4.0, stems from the famed German engineering. The German government, as also leading industrial powerhouses like Robert Bosch and Siemens unveiled the basic concepts and recommendations in the Hannover fair to be adopted by industry worldwide. German manufacturing powerhouse. Siemens led by implementing an Industry 4.0 solution in medical engineering. New software and steering solutions enable Siemens to produce an implant within 3 to 4 hours. Predix, the Operating System (OS) for the Industrial Internet, is powering digital enterprise businesses that drive the global economy.
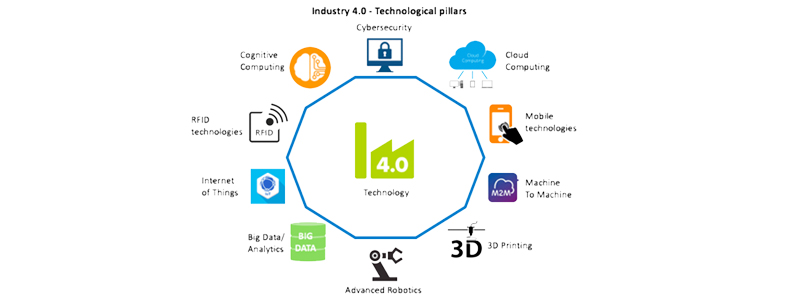
MSME Sector in India
Micro, Small, and Medium Enterprises (MSME) sector has emerged as a vibrant sector of the Indian economy over the last five decades. MSMEs contribute more than 29% to the GDP and are responsible for 50% of the country's total exports. It is accountable for one-third of India's manufacturing output. MSMEs are complementary to big industries as ancillary units, and this sector contributes enormously to the socio-economic development of the country. The MSME segment includes various verticals and sectors, including services, and the recent governmental classification scheme for MSME has also widened the net as also provided larger benefits accrued to the MSME. As per the MSME ministry’s annual report of 2021-2022, there were 65 lakhs+ MSMEs registered in the Udyam portal at the beginning of 2021, but the actual number is in the order of 10 times that number in sectors including manufacturing, services, and trades. 99% are micro, with 0.52% small and 0.1% medium. The number of jobs in the MSME sector is estimated to be 15+ crores. Over a period of time, through MSME-friendly policies and initiatives, it is envisaged that MSME will contribute 50% of the GDP and 75% of exports of the country.
Digital Transformation
Indian MSMEs are steadily moving towards technology adoption and usage. MSME’s software deployment is primarily restricted to stand-alone packages for finance, HR manufacturing, or payroll. There has been a visible digital shift in channels for communication, marketing, payments, hiring, and other business verticals. A minuscule percentage of MSMEs are harnessing Industry 4.0 technologies. Challenges faced includes working capital, trained manpower resources, and lack of awareness or having a comprehensive ICT strategy.
Recommendations for MSME Clusters towards Adoption of Industry 4.0
- This article provides recommendations to MSMEs for adopting Industry 4.0 technologies. This is very relevant considering the fact that there is a significant digital divide between big industry and MSME. Most of the MSMEs fall into the group of low digitalization and low data-driven companies. This is a trend not only in India but even in developed economies.
- The adoption of Industry 4.0 technologies provides immense benefits to industries and MSMEs and gives them opportunities to transform their supply chains into value chains. No doubt, at the initial stages, some of these technologies may be out of reach for individual MSMEs due to the cost and the fact that these MSMEs may also face liquidity issues. MSMEs may have to look for alternatives for short-term financing that can provide assistance for fixing credit issues and enhancing financial performance. The scarcity of loan-granting institutions other than nationalized banks poses another challenge. However, a cluster-based approach towards procurement and adoption of Industry 4.0 technologies can prove to be beneficial to them if these procurements are done as an MSME cluster. Total Cost of Ownership (TCO) will reduce for these MSMEs.
- An added advantage is that most of the MSME clusters are well-organized. To cite an example, CODISSIA, Coimbatore District Small Industries Association, boasts more than 2000 members in 43 sectors. A world-class trade fair complex as an industrial and exhibition venue and incubation center for defense are some of the achievements of this cluster. Likewise, there are many similar success stories pan-India. Another cluster representing the pump, foundry, and motor sectors in the Coimbatore region is the Southern India Engineering Manufacturers' Association (SIEMA) has 300 members.
- In terms of software packages in AI and/or IoT as part of Industry 4.0, these packages can be sold as a cloud-based solution to the MSME. This would reduce the TCO as the MSME need not procure expensive servers, hardware, and/or infrastructure to host the software package.
- Exploring open-source packages and menu-based approaches is also an option. In other words, procure the required modules from the software package as per need and top up as required. However, these targeted digital improvements need to be focused and dovetailed into the strategic roadmap of the MSME.
- MSMEs can incrementally procure Industry 4.0 technologies. They can start small by starting with apps, sensors & IoT and then move up the value chain to high-end robotics, AI, and the like. This results in the optimization of resources. Pilot projects can be pursued as proof-of-concept and implemented in localized value chains.
- Considering the rapid growth of digital technologies, regular upskilling, and training programs for employees in MSMEs are absolutely necessary. Their domain knowledge, coupled with their expertise in analytics and the link, would be an excellent combination.
- Awareness needs to build from top to bottom of the organizations such that not only the top management but employees at all levels champion the adoption of Industry 4.0. This awareness would also propel top management to make the necessary investments toward procurement of other digital technologies. Data management and associated policies must also be formulated and communicated to all stakeholders.
- MSMEs should target external value chains first by utilizing commercially available Industry 4.0 tools in the e-commerce and logistic sectors. Batch and continuous manufacturing MSMEs will be the early beneficiaries of Industry 4.0 solutions as compared to those involved in the process and discrete manufacturing. This is because they rely on an established Bill of Material (BOM) and defined work processes in the form of assembly lines, while process manufacturing relies on a process formula.
Undoubtedly, Industry 4.0-enabled MSMEs have a huge opportunity for growth and success. This is the right time for MSMEs to embrace Industry 4.0 so as to bring about dramatic improvements in their performance. This will go a long way in streamlining their processes & support systems digitally, bringing in automation, and leveraging big data toward customer satisfaction. Using these recommendations, the next course of action would be to develop a framework on the factors that affect the adoption of Industry 4.0 in MSMEs and empirically capture their contribution towards the organizational performance of MSMEs.
About the Author
Dr. Prashant R. Nair is the Vice-Chairman of IQAC & DST-AMRITA Technology Enabling Center (TEC) Fellow, Amrita Vishwa Vidyapeetham, Coimbatore.